Foresters spend their careers growing trees for the lumber needs of future generations. To celebrate the end use of our work, we created the Rayonier DIY Contest for woodworkers, seeking to see some of the best DIY projects around. We started with our own team. Today, we feature our grand prize winner: Washington State-based Resource Land Manager Neris Biciunas and his entry of traditionally made wooden kayaks.
When we launched our Wooden DIY Projects Contest for employees during the 2020 pandemic lockdowns, we had no idea just how talented our Rayonier employees were at woodworking.
From hand-carved tables to cider presses, wooden coolers, workout benches and everything in between, the task of choosing a winner from such a creative and resourceful bunch was a tall order.
However, one project stood out as the overall fan favorite: Traditional East Greenland Style Kayaks built by Resource Land Manager Neris Biciunas.
We caught up with Neris, who’s based in Forks, Washington, to get the story behind what goes into crafting these buoyant beauties, and learn more about his journey to woodworking.
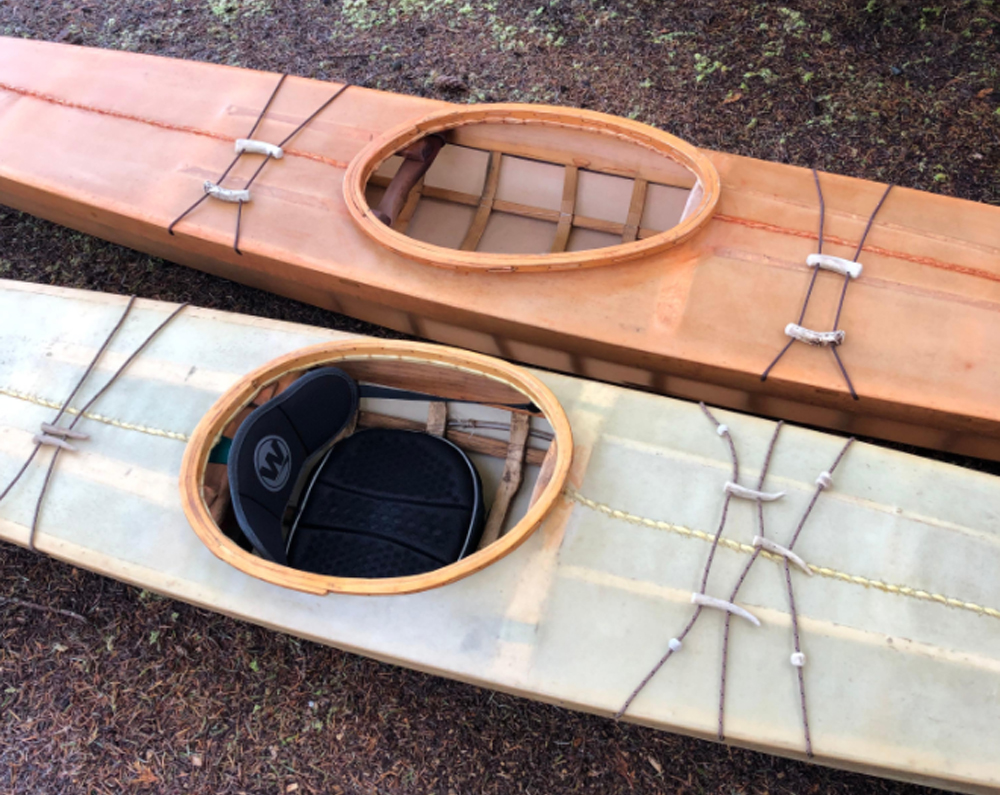
Building kayaks began as a family affair
Whilst admiring these kayaks, you’d never believe they were hand-constructed in a self-taught hobbyist’s garage over the course of a few weekends. But that’s exactly how they were made.
“When people look at the kayak I made, they think: That’s epic and must have taken you forever! But the truth is, most of the instructions came from a book. The rest came from the wisdom of the internet, and I simply took it one piece at a time,” Neris says.
He started woodworking as a hobby several years ago. As soon as he had a place to work and his daughters were ready to start playing in the water, he began building wooden kayaks.
“I could have followed the path of kayaking as an individual sport, but I made a deliberate choice to include my family. And it’s nearly impossible to buy a kayak for a small person no matter how much money you have. So that pointed me toward building something, because I can build a scaled-down kayak for a small person.”
Neris’s daughters, now 17 and 20, learned to kayak from a young age.
“Sea kayaking is pretty easy because you don’t need rapids or a three week expedition, and it gave them a chance to learn about doing it safely from an early age. When they outgrew their kayaks, we could pass them on to other growing families.”
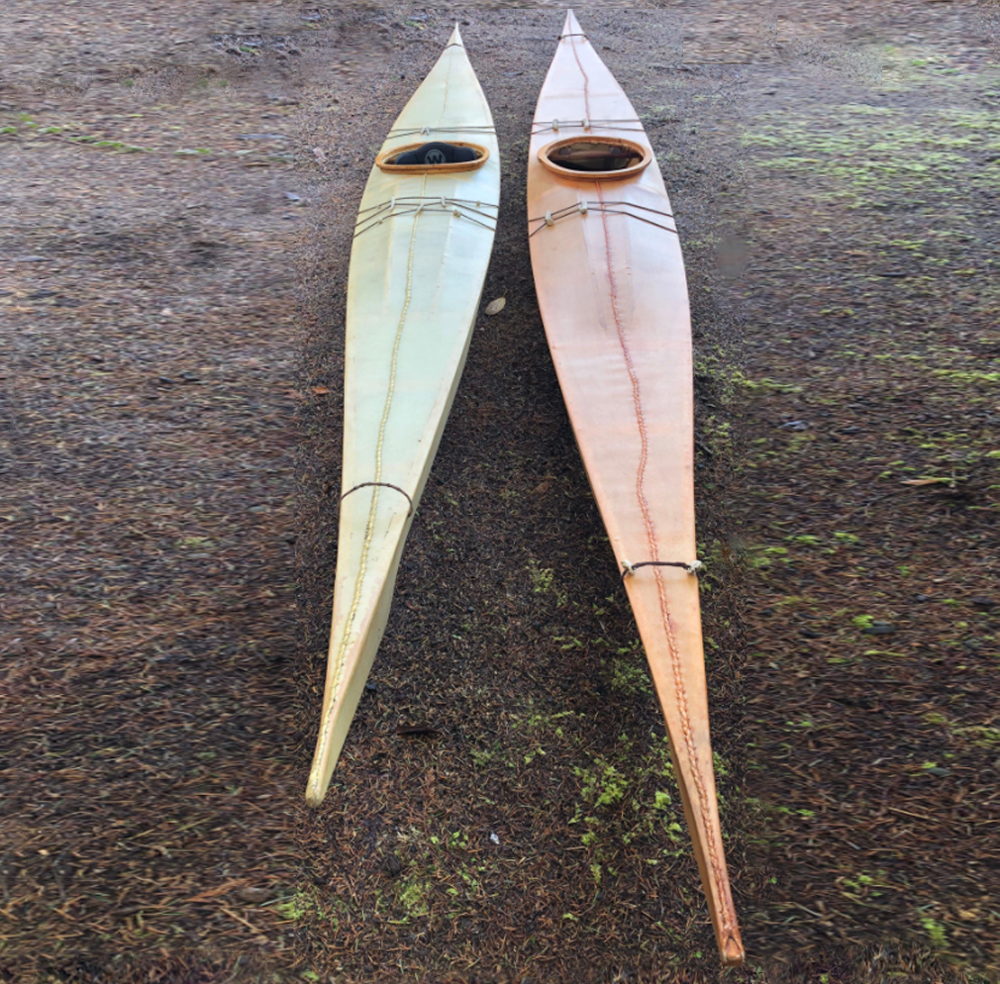
The history of wooden kayaks and their traditional craftsmanship
The only thing more enchanting than looking at these kayaks is learning about their history…which Neris tells with enthusiasm.
“Kayaks originated as a very efficient hunting vehicle for people in arctic areas—and they had to be efficient or they’d go hungry. What’s really interesting is they had very few resources to build with…they didn’t even have trees up there! So the first question is: where do you get lumber? They’d use driftwood. They also didn’t have nails, bolts, glues, or high-tech materials so a large piece of driftwood was split into many smaller pieces for the structure, the occasional bit of bone material for a joint, animal sinew [tendons] for lashing parts together and seal hides for the outer coating. And that’s why many people call this style ‘skin on frame.’”
Applying traditional techniques to contemporary kayaks
For his modern kayaks, Neris blends traditional building techniques with contemporary materials. Either nylon or polyester fabric with a certain type of varnish or paint mimics the function of a seal skin.
“For my daughters, I used a canvas material for a skin because I can seal it with an exterior house paint. And I used nylon for the bigger kayaks. The joinery is a combination of things. Dowels or mortise and tenon make most connections. Many parts are lashed together. The ‘skin’ also contributes to strengthening the whole craft. ”
For sourcing the wood (Douglas-fir, Western Red Cedar, Port Orford Cedar, Pacific Yew, and Vine Maple), Neris has found certain pieces at the local saw mill, his woodpile and the hardware store. He sources specialty pieces, like curved wood, directly from the woods (including Raynioner slash piles).
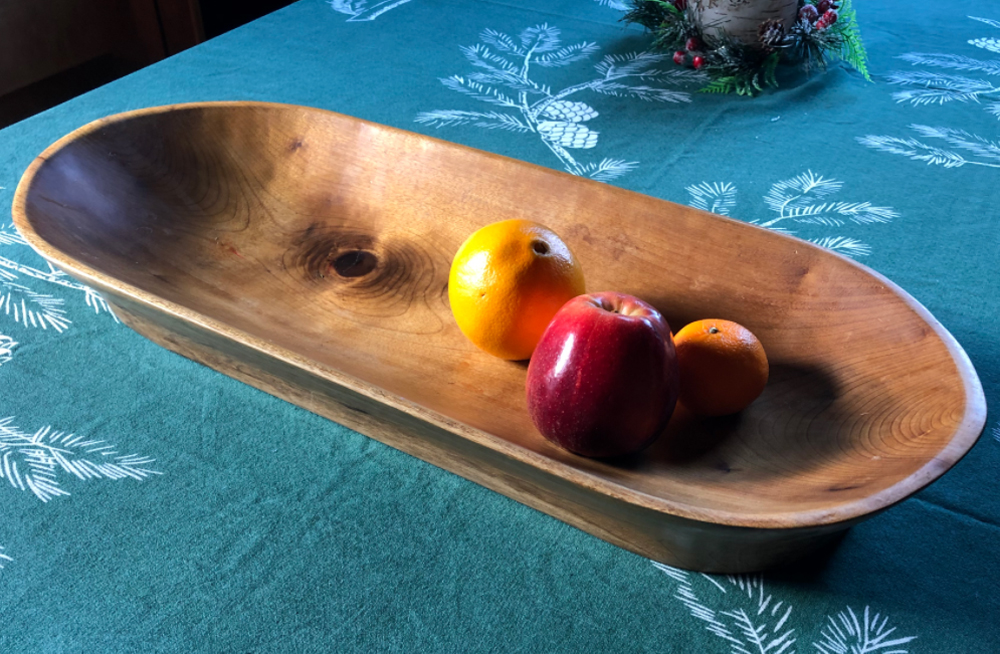
The “why” behind the hobby
Everyone has different reasons for pursuing woodworking. For Neris, it’s mostly about the opportunity to learn something new.
“It is also very relaxing to whittle away at something. Part of that learning process is studying the idea and looking at alternatives and thinking about how I can accomplish this with what I have for materials and skills. I like to think of it as learning and understanding, and by practicing I increase my level of understanding.”
Some of his other favorite projects include a cider press, the bread kneading trough shown above, a wood-based workout station, and skim boards.
Neris gave an example of that deepened understanding and experimentation when sharing about his favorite piece he ever made, a kayak for his wife. In need of a 20 inch piece of wood to manipulate into a U-shape, something that’s typically done with a large steamer, Neris used a piece of vine maple which he heated in the microwave to achieve the same result.
“I took it out of the microwave and it bent like a wet noodle! You can’t build furniture with a microwave, but it worked great for a kayak. And that kind of goes back to looking at the process and thinking, ‘How else can I do this with what I have?’”
This spirit of working with what you have seemed to be universal among all the top Rayonier Woodworkers. The bottom line: you don’t need expensive equipment or a lot of space to create amazing wooden art.
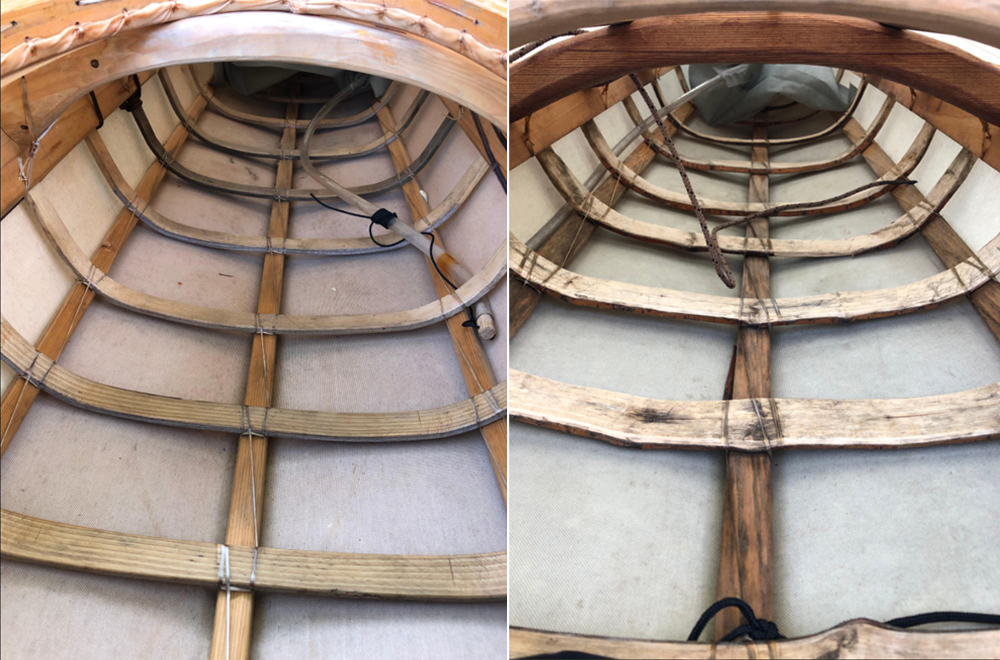
Neris’s advice for aspiring woodworkers: pick a target and do it
When asked what advice he would give aspiring woodworkers, he replied:
“Pick a target and do it. Start appropriately for your skill level and build on your experiences. Woodworking is very friendly toward little increments, little steps at a time, little pieces at a time.”
He also recommends Instructables.com, which features plans for wooden kayaks, along with many other beginner, intermediate and advanced-level projects.
On behalf of the entire Rayonier team, congratulations Neris! He won the overall fan favorite award and the large outdoor category.
You can read more of our DIY stories featuring talented woodworkers here.
Leave a Comment