We put decades of work into each stand of trees, all leading to this day. Join us “behind the scenes” as we harvest them and turn them into logs destined to become all kinds of products you depend on every day.
KINGSLAND, Georgia—Did you know a single tree might be used to produce multiple products, such as lumber, plywood and paper pulp?
A harvest operation does not simply involve taking trees and loading them onto trucks. Rather, they are carefully inspected one-by-one, sorted by size and quality, cut to specific lengths, and sent to different facilities depending on what they are destined to become.
The most important role in a harvest is that of the loader operator. With a trained eye, he or she can determine how to sort the logs without ever stepping out of the cab of the loader. The operator must judge the logs’ diameter, straightness and overall form to determine how to cut them and what products they will ultimately become.
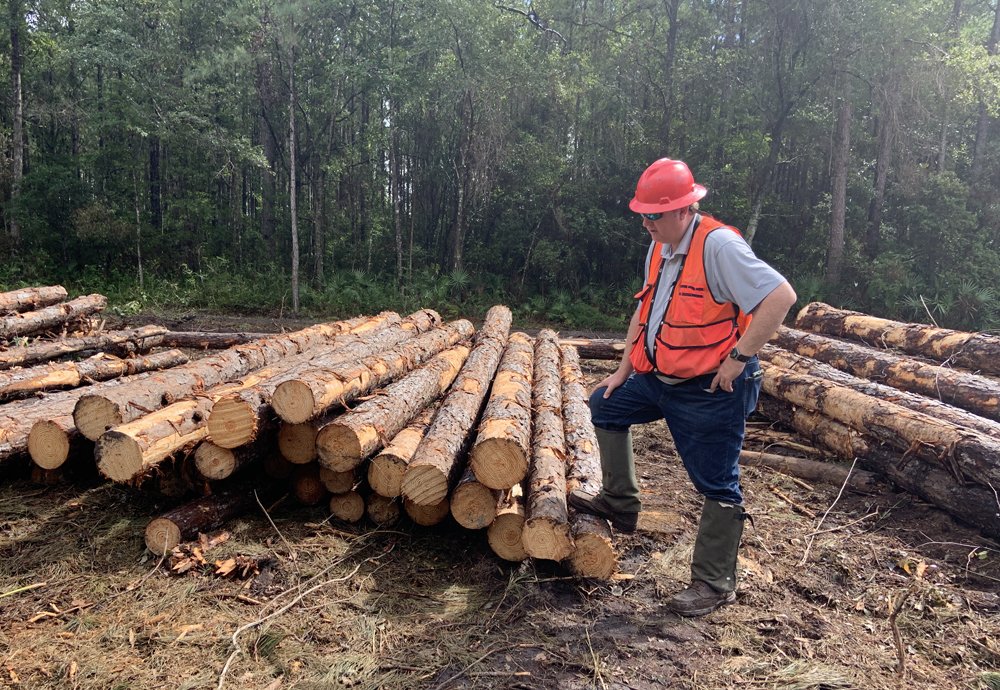
One Tree Makes Many Products
During a recent harvest, Timber Marketing Manager Rusty Cobb walked the length of one tree that had been set aside for demonstration purposes. He explained that single tree would be cut into three pieces:
- Thanks to its large (above 8-inches) diameter and its straightness, the first two 19-foot, 5-inch sections of the tree would make excellent export logs. This is the most valuable use for logs on this property.
- The skinnier top of the tree didn’t have enough diameter to become an export log. Instead, it would become a 25-foot chip-n-saw log, used to make boards and paper pulp.
A loader operator makes the same type of determination for thousands of trees during the course of the harvest. Different log sorts will be loaded onto different trailers, which will then be driven to various mills or export yards.
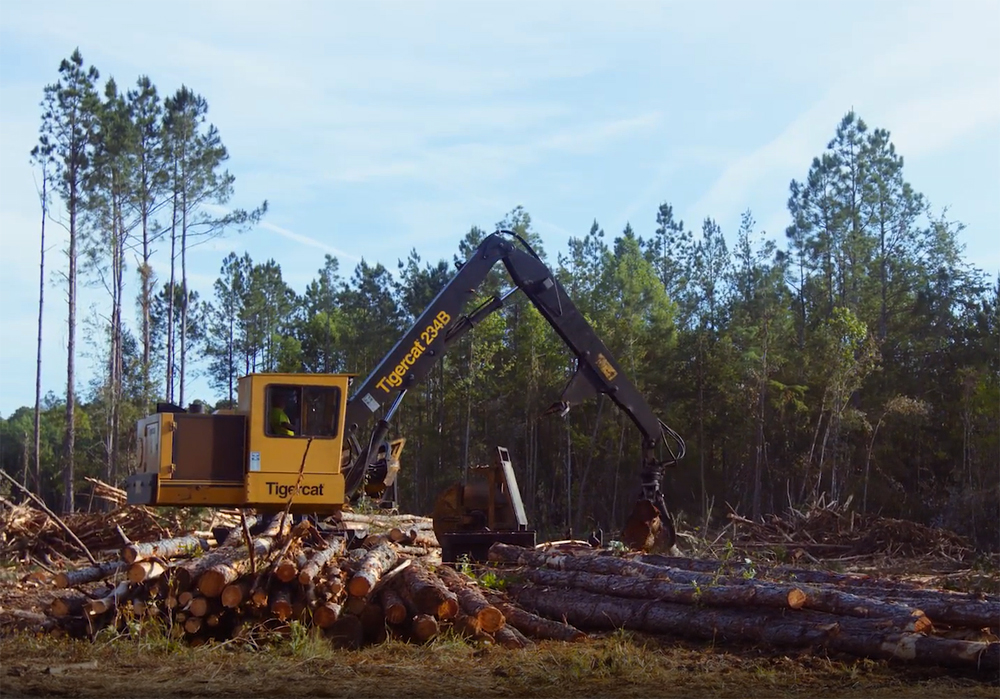
Types of Products Southern Yellow Pines Become
Here are the products Rayonier’s Southern Yellow Pine forests are typically sorted into, in order from most valuable to least:
- Export logs. These high-value logs are cut to shipping container length, then they’re shipped to countries in other parts of the world, which use them to make lumber and veneer.
- Poles. Also meeting very specific standards for straightness, size and quality, these logs are destined to become utility poles or pilings for structures like docks. Watch how our foresters identify poles in this video.
- Domestic Saw Timber. The next-best use for a large, straight log without defect is domestic saw timber. These logs are made into larger lumber, such as 2X10s and 2X8s.
- Chip-N-Saw. These logs are used to make smaller cuts of lumber, like 2x4s and 2X6s, with leftovers chipped and used for pulp.
- Canterwood. While smaller and thus less valuable than Chip-N-Saw, canterwood makes small boards. Again, the rest of the wood is chipped and used for pulp.
- Pulpwood. The logs used for pulpwood are smaller in diameter and / or crooked, knotty or flawed, thus not ideal for making into lumber. Pulpwood is broken down into pulp, then made into paper and thousands of everyday products. You can read about many of the little-known products made from pulpwood here.
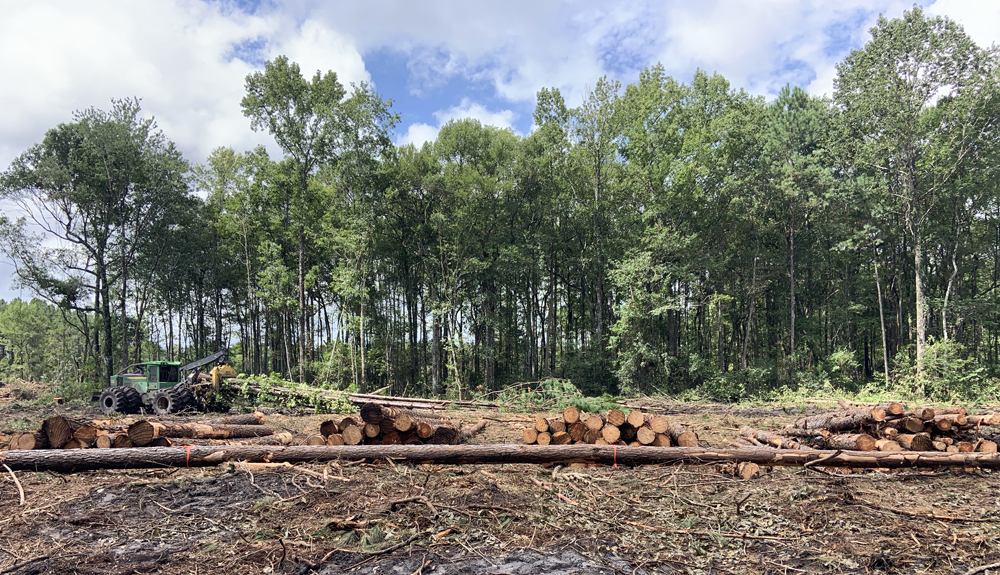
The Result of More Than 20 Years of Work
So how did the trees get to this point? Here’s a quick overview of the work our foresters put into it:
- A specific group of trees called a stand was planted in this location by a forester 20 years or more ago.
- Over the decades that followed, our team kept an eye on how the forest was progressing. Early in its lifecycle, we may have used herbicide to eliminate competing weeds that would have killed the trees or stunted their growth.
- We may have given the trees fertilizer as needed over the years to encourage their growth.
- If we saw any sign of disease or insect infestation, we worked to eliminate it as quickly as possible.
- And about 10-15 years after planting, we thinned the forest, taking weaker and diseased trees to the pulp mill. That left more space for the strongest trees to grow to their full potential.
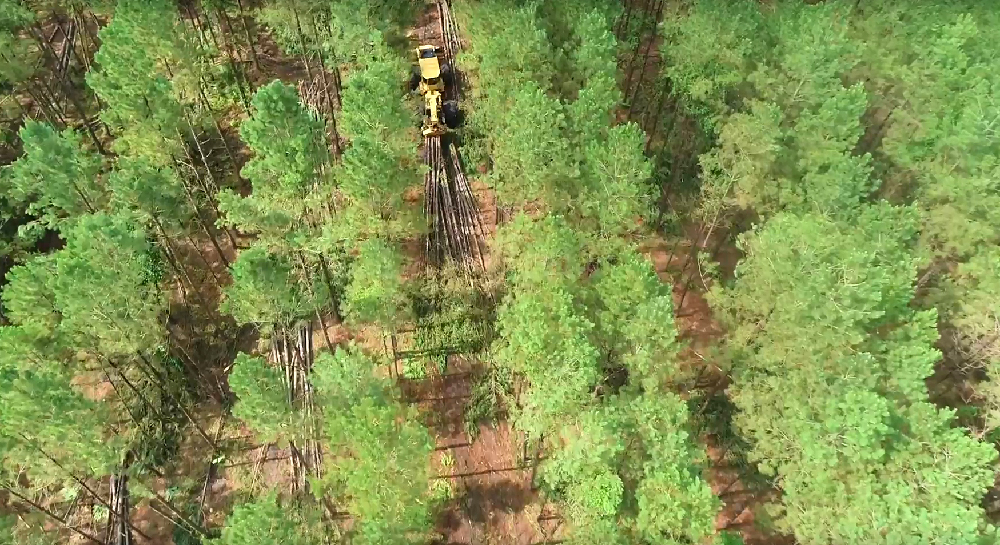
As a Timber Marketing Manager, it’s Rusty’s job to make that 20+ year investment pay off. To do that, he estimates what types of products are in the stand of trees even before the harvest begins. He does this by measuring plots in the timber stand (see his demonstration of a timber cruise here). Once he has an idea of the value, he can either directly sell the timber to various facilities, hiring a logging crew to harvest and deliver the timber, or he can sell the standing timber to a dealer who will then manage the logging and sales to the mills.
What Happens After a Timber Harvest
Once the harvest is complete, planning for the next generation of trees begins. If needed, the land will be prepared through raking or chopping debris to break it down; plowing the soil into long mounds if the water table is high; and then planting the next stand of trees, ideally within a year of the harvest. Then the cycle begins all over again, with foresters nurturing that forest for another 20+ years until it’s time to harvest again. Laid out like a patchwork quilt in the forest, each stand of trees is at a different stage in the lifecycle, allowing a richly diverse habitat for the wildlife of the forest and ensuring a steady supply of wood for generations to come.

Leave a Comment