Follow the journey as a group of trees from a Rayonier forest become 2×4 and 2×6 boards at a West Fraser sawmill. Lumber is primarily used to build new houses and in repair and remodeling projects.
Did you ever look at a smooth, straight board and wonder how it could come from a tree? What happens to the bark and branches? How can it be so straight, when trees sometimes aren’t?
Today we’re going to see what happens from the moment a tree is harvested to the point its lumber is store-ready. This is the process that makes it possible to build homes, frame concrete, create DIY projects and do countless other tasks with wood.
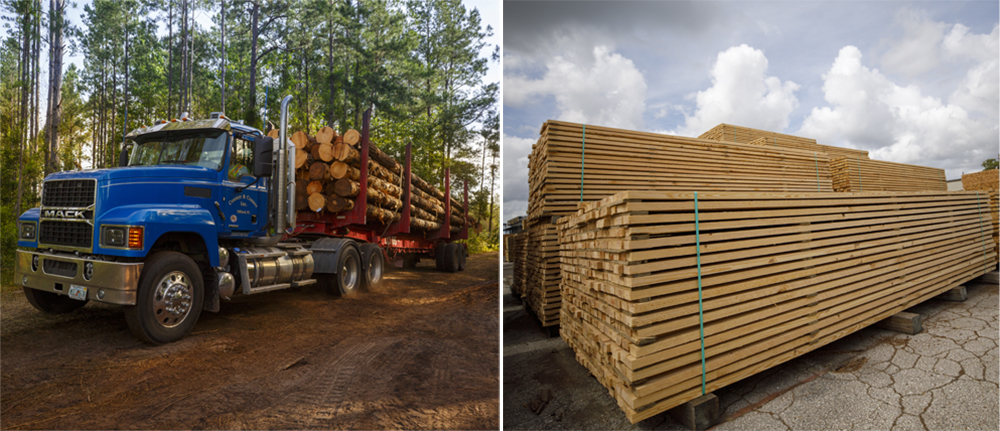
Step 1: Growing the right trees the right way
For a forest products company, the first step is the most time-consuming part of our business. Growing the right trees takes decades!
Our scientists ensure we plant only the best tree families. They choose the families that grow the straightest and resist disease and insects the most. Both “parents” are accounted for in controlled pollination, a process that allows us to determine which pollen fertilizes the pinecones in our seed orchards. You can see a video of how controlled pollination works here.
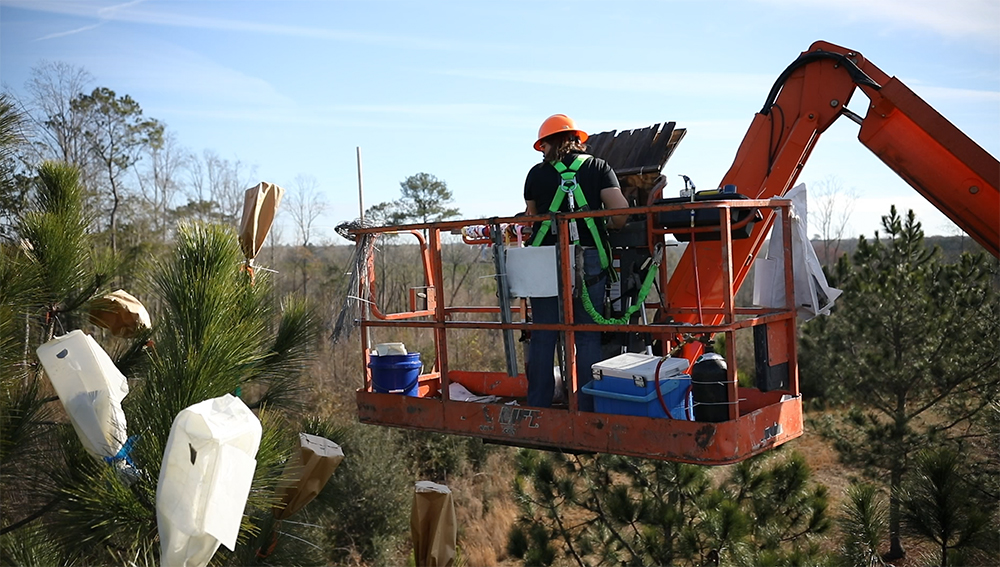
Foresters known as Resource Land Managers plant the trees quite close together, which encourages them to grow tall rather than producing a lot of excess branches. That’s important because branches make knots in the wood, weakening it.
We nurture the forest, monitoring its growth and addressing any needs the trees may have for decades. Halfway through their lifecycle, we may “thin” the forest, removing unhealthy trees and trees that are too crooked to make good lumber. This gives the best trees more room to grow. Watch our video of a thinning operation to see how the spacing improves.
In the U.S. South, where we grow Southern yellow pines, trees destined to become lumber grow for about 20 to 25 years. In the Pacific Northwest, where our forests are primarily made up of Douglas-firs and western hemlocks, our trees may grow 40 years or longer.
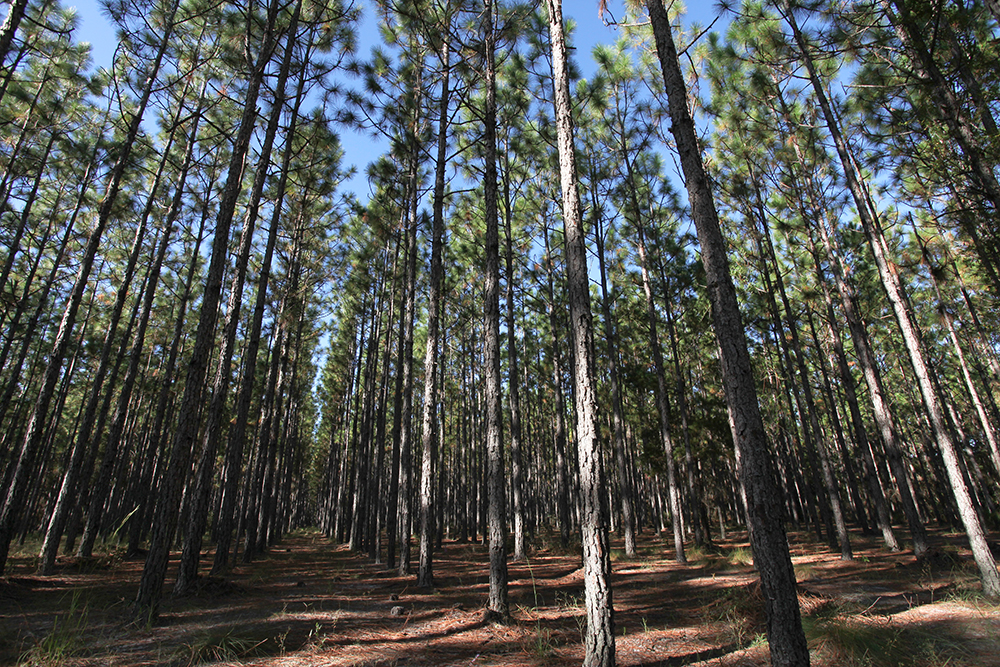
Step 2: Harvesting and sorting the logs
When it’s time to harvest the trees, foresters we call Timber Marketers work to find the best buyer. They want to get the best possible value out of the investment we put into the forest. Timber Marketers often work directly with nearby facilities, hiring loggers to prepare and deliver the logs to mills and exporters. They also can sell the standing timber to a dealer, who will then manage the logging and sale of the logs.
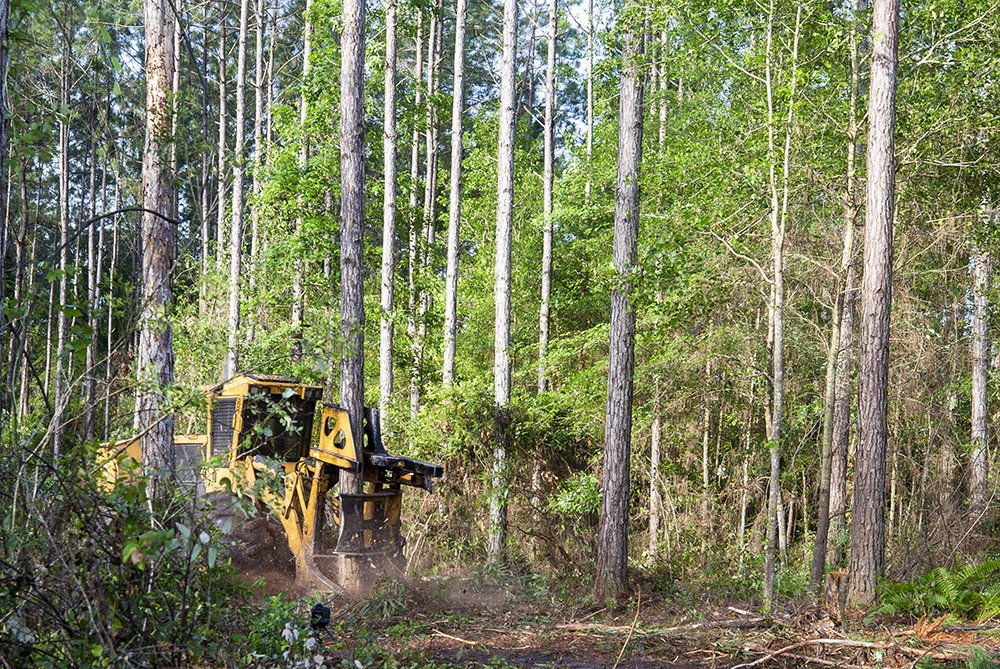
Today, we’re showing you what happens when we work directly with a customer. In this case, Timber Marketing Manager Rusty Cobb is selling a stand of loblolly pines in Kingsland, Georgia. He sells logs directly to the West Fraser sawmill in Whitehouse, Florida. The logs have to meet West Fraser’s standards for length, diameter, straightness and quality. Rusty hires Conner & Conner, a small logging company out of Hilliard, Florida, to harvest and prepare the logs.
As the heavy equipment operators begin to harvest the forest, they keep in mind where the logs will be going. In the same forest, there will be some smaller or crooked logs that will be broken down into pulp for the paper mill. Others will become export logs. In this case, West Fraser’s logs will become lumber. It is up to the equipment operators to visually judge about 1000 logs per-day and decide where they will go.
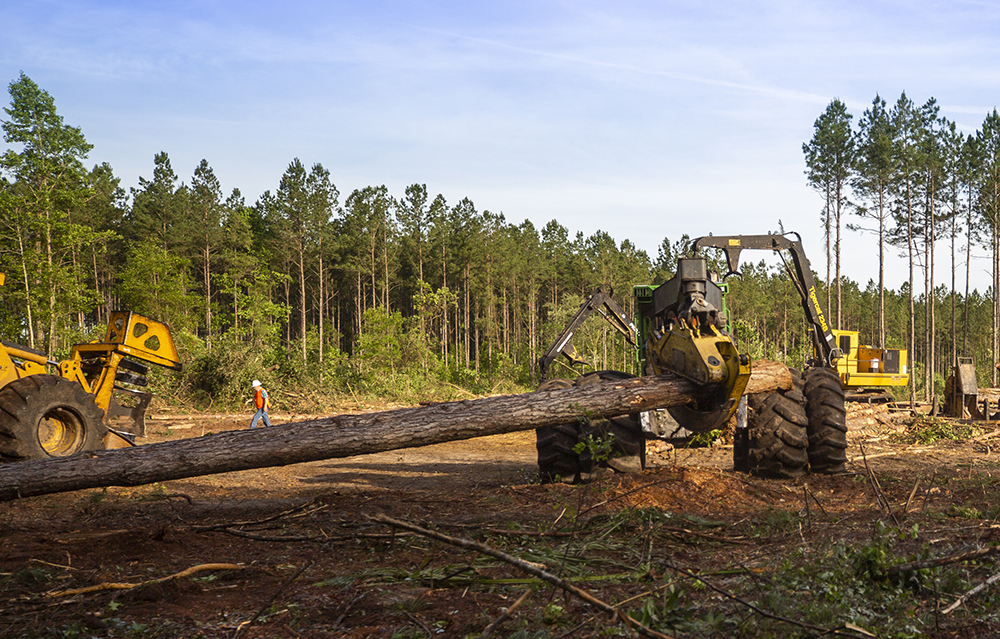
The feller buncher operator, who cuts the trees, tries to group similar products (logs of a relatively uniform size and quality) together during the cutting process. Then the skidder operator drags the logs to a landing area, where the loader operator makes the final decision where each log will go.
The loader operator processes the logs to the correct size and condition the buyer wants. First, they’re cut to the right length. Then, lifting the logs in the loader’s knuckle boom, the operator can pull the logs through a set of fixed knives, which remove large limbs and some of the bark. The logs are then loaded onto a log truck and strapped into place. You can learn more about this stage in the process by watching our video, What Happens During a Timber Harvest.
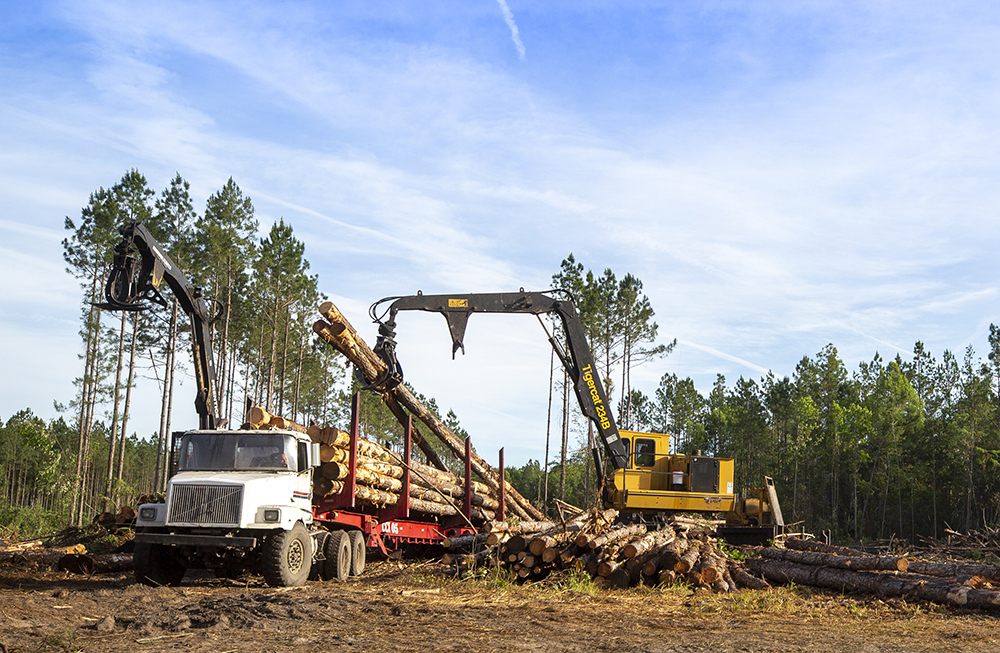
Step 3: Processing at the Sawmill
When the log truck arrives at the West Fraser mill, it drives onto a scale, where it’s weighed. The load of logs is also inspected by mill employees called scalers, who ensure the logs meet the mill’s standards.
After the logs meet the scalers’ approval, the truck moves to an unloading area, where a special machine that looks like a huge forklift unloads the logs. Once it’s time to process the logs, they’re placed in a debarker machine that removes the rough bark from their exterior. Then they enter the “cut-ups” or “bucking” process, which involves cutting the logs to the right length.
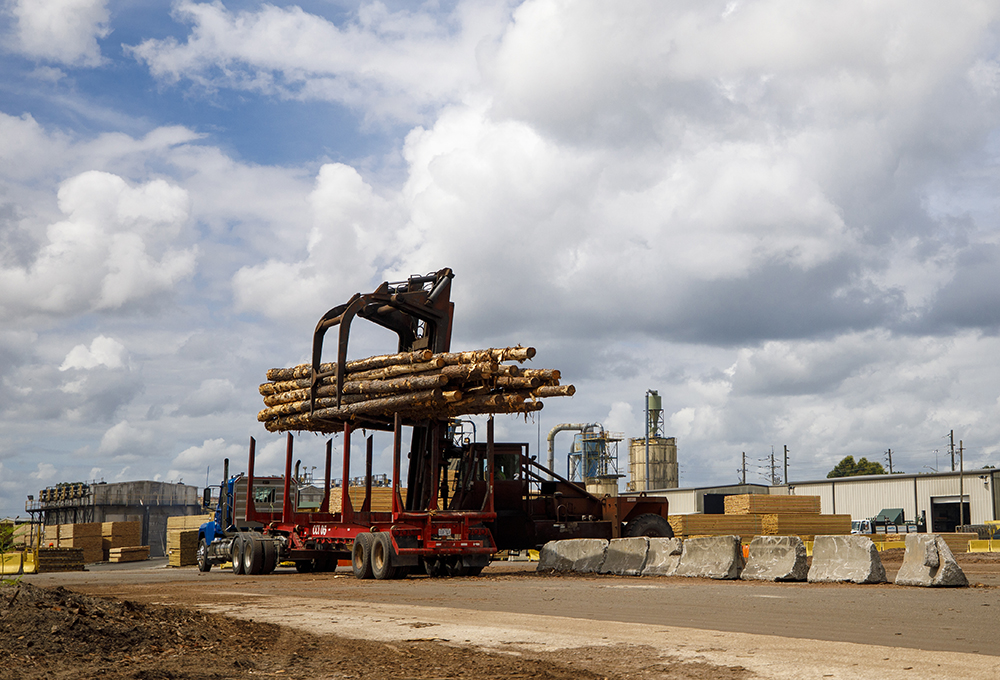
The next step is shaping the round logs into squares, a necessary step before cutting them into lumber. The canter line removes the least possible amount of wood from the logs to reshape them. But nothing goes to waste. The removed bark becomes a mulch product, while sawdust is used in making wood pellets.
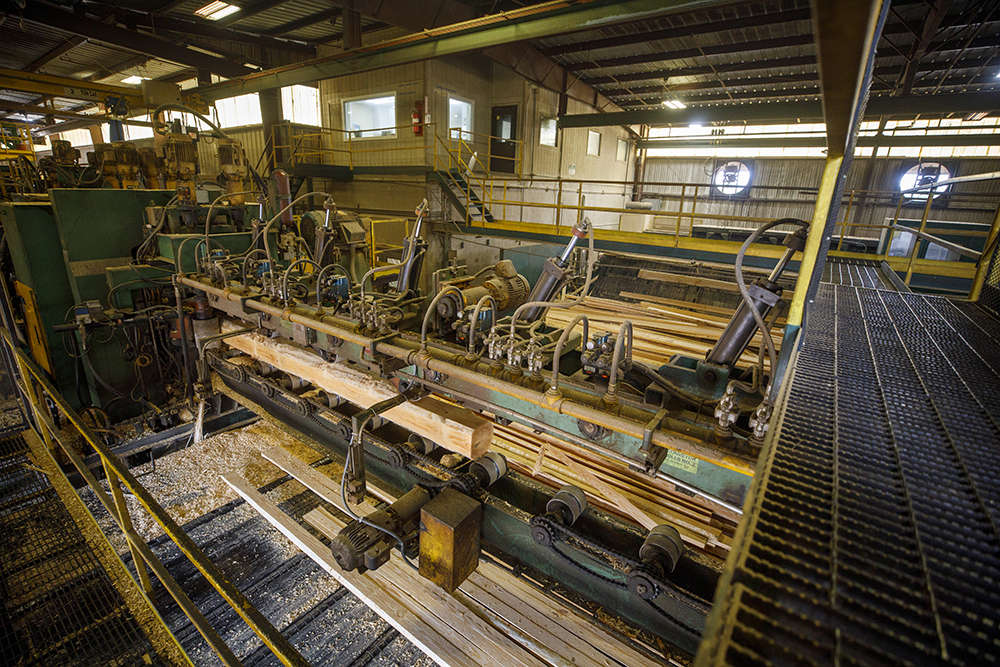
The process gets really high tech with the VDA saw. Using highly-sensitive scanning equipment, the saw can cut the logs into board widths that are accurately sized within thousandths of an inch. The saw automatically optimizes each log to cut the most possible high-demand sizes of boards without wasting any wood. It also analyzes the logs for defects to ensure issues like severe knots don’t ruin the resulting cuts of lumber.
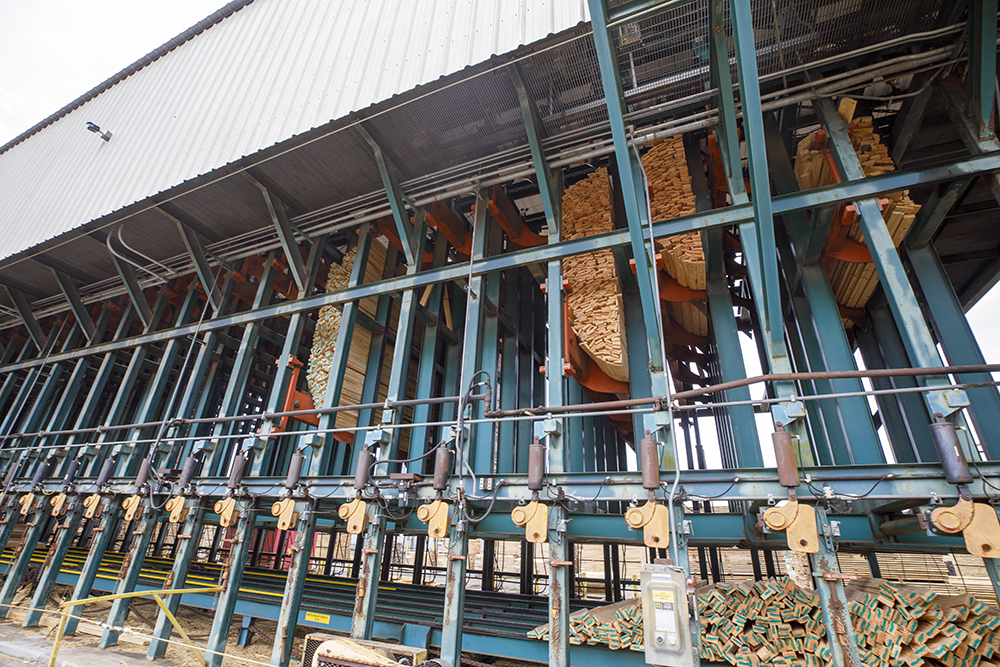
The green trim saw follows: this saw trims the boards to the right lengths, again cutting around knots and other defects whenever possible. The majority will be formed into 2×4 or 2×6 boards.
In the sort up bays, the boards are grouped by size. Then they are placed in the stacker, which packages them together so they can dry in the 230-degree kiln. This drying process in West Fraser’s three massive 52-foot-long “ovens” removes moisture, preventing warping in the wood.
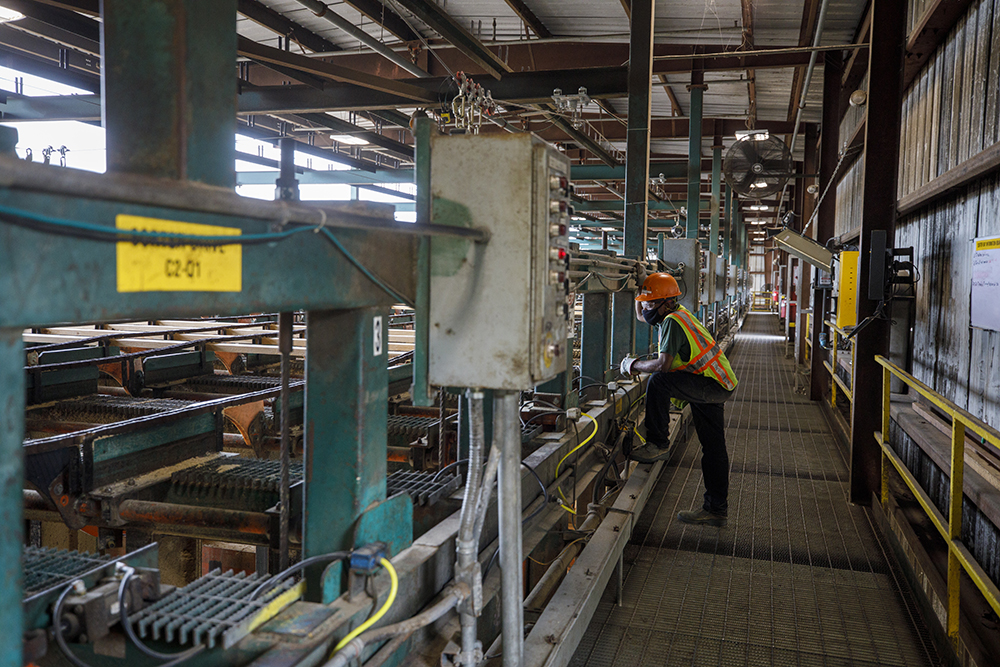
The dry boards then get a final polish in the planer, which smooths their tops and bottoms as they whip through at a speed of 1500 feet per minute.
Finally, the boards are packaged and moved to the warehouse, where they’ll await shipment to nearby stores and businesses.
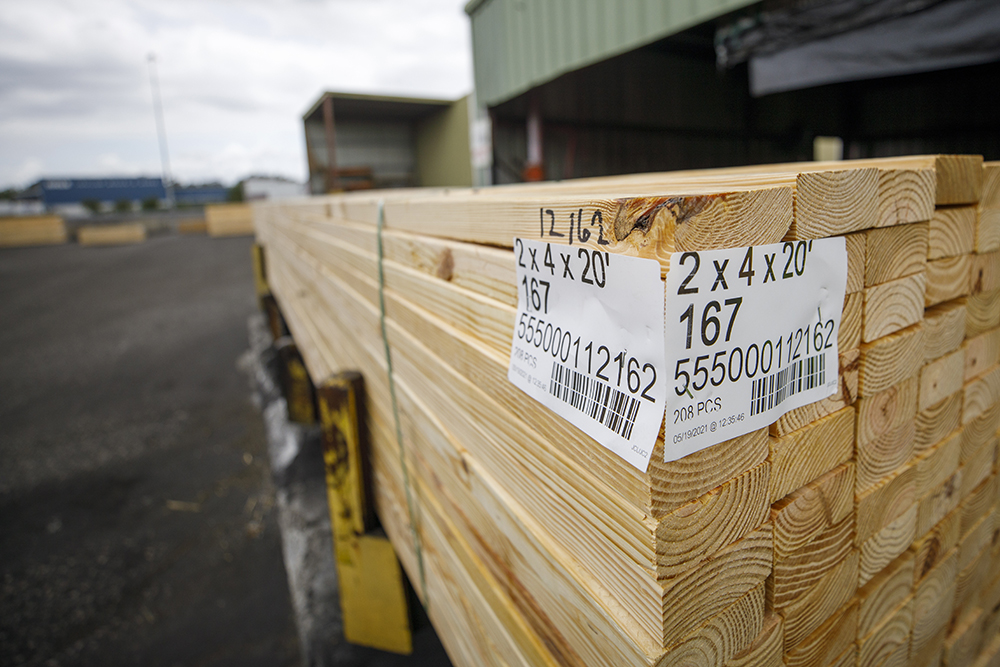
A sustainable process
With as many as a thousand trees being harvested in one day on one logging site, and so many homes and buildings continuously being built around us, it’s only natural to wonder: will we run out of trees? Sustainable forestry is designed to make sure we have a reliable wood supply that won’t run out.
As soon as a mature forest is harvested, our foresters begin making plans for the next forest that will take its place. Typically, within a year of the harvest, the next generation of trees will be planted on that same property. It will be ready just in time for the lumber needs that arise 20 years from now.
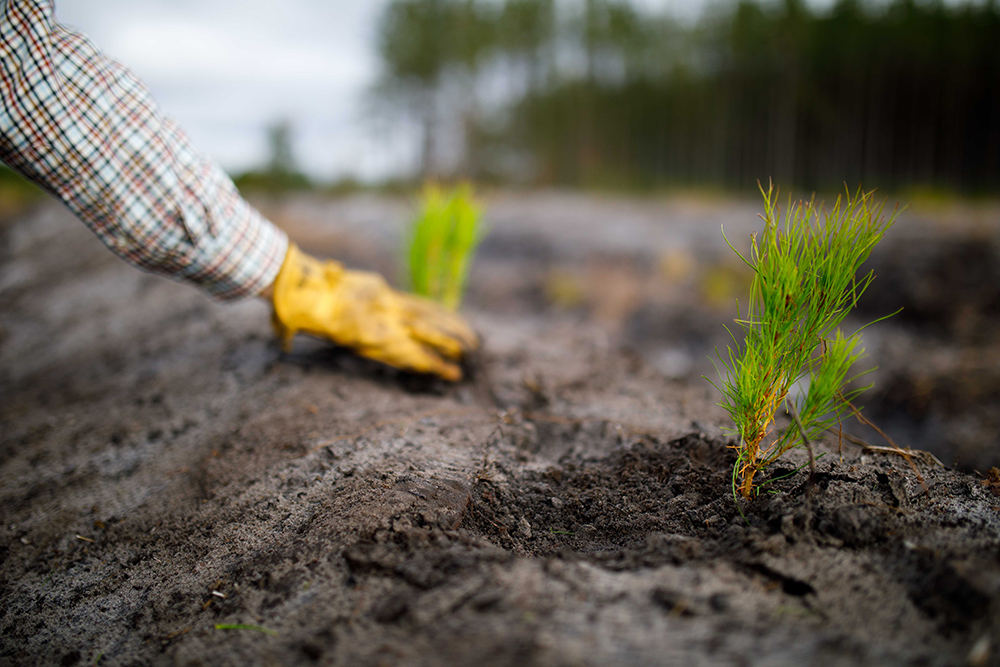
We also safeguard the wood supply by ensuring we only harvest a certain amount of trees in each area each year. The result is a mosaic of different ages of trees in our forests. That not only ensures that there will be a reliable wood supply every year, but it also creates a variety of habitats for the wildlife that lives within our forest ecosystem. Younger stands have more vegetation, like berry bushes and flowers. Older stands offer shade and shelter.
With sustainable forestry, trees do it all: they provide clean air and a home for wildlife during their lifetime. When they’re harvested, they meet countless needs as they become products like lumber and cardboard and paper goods. They’re also used to make cellulose, an ingredient in 1000s of products, including medicines, paints, foods, even touchscreens. And all the while, when trees become products, they continue to store carbon for the lifetime of the product they become. It doesn’t get any more sustainable than that!
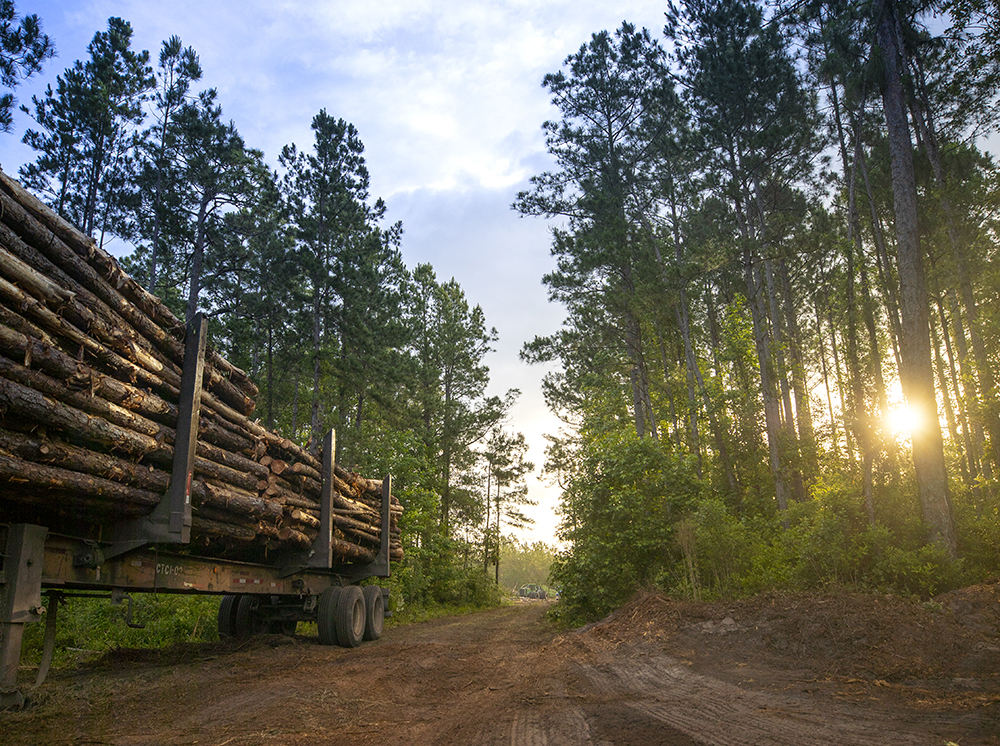
Leave a Comment